Autor
José Ignacio Linares
Director de la Cátedra Fundación Repsol en Transición Energética en la Universidad Pontificia Comillas (ICAI)
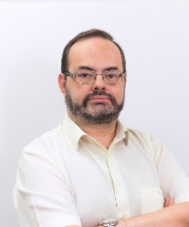
Autor
Ángela González
Estudiante del Máster de Ingeniería Industrial
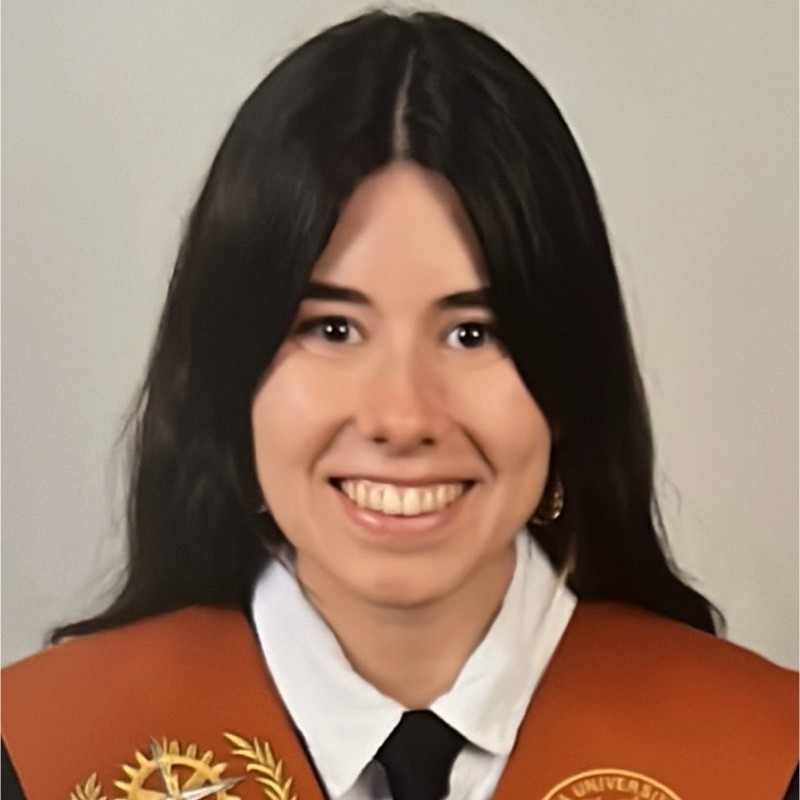
Aprovechamiento del Calor Residual en Procesos Industriales
El aprovechamiento del calor residual de procesos industriales, como las torres de refrigeración, puede aumentar significativamente la eficiencia energética global. 🌍
Potencial del Calor Residual
El calor residual a media/baja temperatura es crucial para descarbonizar la demanda térmica de muchas industrias (textil, alimenticia, papelera, química…). Un uso potencial es su conversión en vapor, esencial para actividades industriales como la generación de electricidad, la esterilización, el procesamiento de alimentos y la climatización.
Torres de Refrigeración y Consumo de Agua
Las torres de refrigeración disipan el calor del fluido circulante, pero consumen entre 2 y 5 m³ de agua por cada MWh transferido, lo cual puede ser limitante en épocas de estrés hídrico. 💧
Solución Propuesta: Bomba de Calor de Alta Temperatura
Instalar una bomba de calor de alta temperatura en procesos industriales puede:
- Reemplazar las torres de refrigeración y su consumo de agua.
- Producir vapor, aumentando la producción de electricidad en la turbina de cogeneración.
Análisis del Estudio
El estudio analiza el aprovechamiento de una corriente de calor residual a baja temperatura (60-70°C) para producir vapor mediante una bomba de calor de alta temperatura basada en un ciclo inverso de Brayton con CO2. Esta solución permite:
- Enfriar la corriente de agua caliente, suprimiendo las torres y ahorrando agua.
- Alcanzar una temperatura de salida del agua más baja, facilitando su tratamiento.
- Producir vapor de proceso, eliminando una extracción de la turbina de cogeneración y generando electricidad adicional.
Resultados del Estudio
Se consideran dos escenarios principales basados en el calor residual disponible y las condiciones de generación de vapor. En las mejores condiciones, se consigue un COP de 2,03. La planta tiene dimensiones de 21m x 21m x 25m y requiere una inversión de 44.383.762€, con un coste de 611€/kW.
Costes y Viabilidad Económica
- Costes de Calor (LCOH): 51 €/MWh a 62 €/MWh.
- Costes Operativos (OPEX): 43,5 €/MWh a 46 €/MWh. Estos costes son competitivos frente a sistemas ETES, establecidos en 75 €/MWh en 2023, con un objetivo de 63 €/MWh en 2030.
Para conocer todos los detalles y profundizar en el análisis, puedes descargar el artículo completo. 📥 ¡No te lo pierdas!